5 Minutes With Dynabook: IoT's Role in Smart Manufacturing
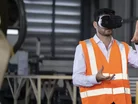
Could you talk me through Dynabook as a business and its activities in the manufacturing industry?
Dynabook Europe GmbH is a dynamic and innovative brand, built on the foundations of its Toshiba heritage. As an industry leader, Toshiba launched the world’s first portable computer in 1985 and followed it up with the world’s first notebook computer in 1989. These two portable computing innovations defined today’s mobile computing market.
Today, Dynabook designs and manufactures its own laptops – right down to the BIOS software that runs beneath Windows. At the same time, Dynabook offers more than just hardware. With its engineering expertise, Dynabook creates and tailors real solutions that integrate the latest technology and design to overcome modern business challenges.
Dynabook’s Windows-based, edge computing device – the dynaEdge DE-100 – is designed specifically for the enterprise to optimise the efficiency of frontline workers. The dynaEdge DE-100 connects to assisted reality (AR) smart glasses to give workers a complete head-mounted display and camera. AR refers to projecting additional information into a user’s field of vision, importantly enabling hands-free working. The manufacturing industry is increasingly adopting the device to empower field workers and streamline workflows.
What are the current trends in the manufacturing industry?
The pandemic has shined a light on the need for manufacturing companies to leverage the capabilities of digital solutions. In fact, according to recent research by Dynabook, 73 per cent of manufacturing businesses in Europe will increase their IT budgets this year. Assistance with business continuity, increased employee productivity and more efficient operations are all clear drivers of this growth in IT provisioning. With increased budgets, Dynabook’s study found that cloud-based solutions (56 per cent), cybersecurity infrastructure (47 per cent) and remote IT support (46 per cent) were highlighted as top IT investment priorities for European manufacturing organisations.
Elsewhere, we’re seeing the cost of raw materials going up, social distancing remaining a priority, and uncertainty around Brexit raising concerns. To meet these challenges, the sector is turning to digital technologies like the Internet of Things (IoT), assisted reality (AR), artificial intelligence (AI) and machine learning (ML) to prepare for the future, and emerge from the pandemic fundamentally changed for the better.
How is IoT currently being deployed in the manufacturing industry?
Wearable technologies like AR smart glasses can enhance maintenance and production by enabling a range of hands-free tasks and processes. For example, smart glasses equipped with a ‘See-What-I-See’ functionality allow an onsite manufacturer, who might have run into difficulty in a time or safety-critical inspection or repair decision, to connect with a wider pool of remote experts and receive valuable support and guidance to complete a task. Additional capabilities from AR smart glasses can be accessed where and when they are needed, without disrupting the mechanic’s workflow.
IoT can also reduce the frequency and duration of human-to-human contact, thereby helping organisations to comply with social distancing measures which may continue in some form post-pandemic. Mechanics can be at a safe distance from each other in the field, wearing AR smart glasses to see exactly what their colleagues can see. Likewise, for tasks like building audits, there is no longer a need to send three or four auditors to a site. One person can be sent wearing a device, and can then feed accurate visuals and information to their off-site colleagues. This is not only beneficial from a health and safety perspective but can support cost reductions and increase efficiency at the same time.
Another area of significant potential is supply chain optimisation and smart capabilities like predictive maintenance. Take for example, when a mechanic is using AR smart glasses to perform a function. If an error were to occur and cause a hold up in the device’s performance, a mechanic’s productivity would be significantly reduced and even cause errors. By combining data from the device in use with other data sources, such as known operational patterns, issues can be identified before they become an interference or danger. The device could alert the mechanic to predicted maintenance and seamlessly be repaired by someone remotely, letting the mechanic continue without any interference.
- The University Manufacturing Circuit Boards from LeavesSustainability & ESG
- Schneider Electric's Commitment to Sustainable ManufacturingSustainability & ESG
- Lenovo & Saudi Alat Building Green Manufacturing FacilitySustainability & ESG
- Manufacturing & Mobility LIVE: Neby Ejigu, FINN PartnersTechnology