5 minutes with: Simon Michie, Pulsant CTO
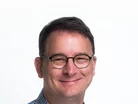
Hi Simon. Tell us, how will edge computing impact the manufacturing sector?
“The potential of edge computing to transform manufacturing is immense. The roll-out of high bandwidth 5G connectivity is steadily bringing industry 4.0 initiatives, the industrial internet of things (IIoT), and artificial intelligence (AI) within the reach of almost every manufacturing plant.
“It is not 5G on its own that will inaugurate this smart, new world of manufacturing – it also depends on a network of highly connected edge data centres at strategic locations.
“By processing data close to where manufacturing operations generate, IT enterprises can locate highly automated, AI-driven facilities almost wherever they wish. Being a long distance from big names in cloud computing is no longer a barrier to innovation because of high latency.”
How does this work with the cloud?
“Edge data centres provide low latency, but they’ve used high-speed fibre to ensure they can still transfer data at scale to the public cloud. This is important because not all data must be processed at the edge of the cloud. Manufacturers will still need to process certain types of data in the public cloud for cost reasons or because they need specific proprietary capabilities.”
Tell us about the convergence of IT and OT.
“Where they process data at the edge, manufacturers will open up a new world of advanced applications. But, at a more strategic level, edge computing will accelerate the convergence of information technology (IT) with operational technology (OT), bringing together systems that run machines, devices and processes with the world of data and analytics. Once they have accomplished this bridge, manufacturing organisations will be able to use standard software and hardware to replace proprietary equipment, liberating them from long innovation cycles.
“OT/IT convergence will transform efficiency using streaming sensor data from the factory floor to optimise power use, raw materials, and human time.
“The data will fuel artificial intelligence applications, robotics, predictive maintenance and prescriptive capabilities. Live data from logistics operations, warehouses and sales will ensure plants meet demand without cost overruns. Smart manufacturing systems in the cloud will remove the costly requirements of on-site control systems in cleanroom environments. Employees can use augmented reality headsets to resolve production line problems more quickly and more cheaply.”
How else can edge technology assist the manufacturing process?
“Digital twin technologies – creating real-time virtual simulations of manufacturing processes with live data – will enable manufacturers to run scenarios to see where they can improve or adapt processes, giving them the confidence to make important decisions very quickly.
“Rapidly growing awareness of these transformational advantages is why market intelligence company IDC estimates discrete and process manufacturing companies will invest US$33.bn in edge architecture in 2022.
“It can, however, be difficult to see through the various configurations proposed for 5G and edge computing, which include small data centres close to phone masts or allied to radio access network base stations. We are already seeing, however, that private, localised 5G networks are gaining popularity with large enterprises such as port operators, while telecommunications companies are fast collaborating with cloud-providers on business-oriented solutions.”
Tell us more about edge data centres and how manufacturers CAN make use of them
“Most advanced manufacturing applications will depend on data from sensors, which are relatively ‘dumb’ devices. The IoT gateways needed to process this data can only do so efficiently and cost-effectively in a fully mature edge data centre.
“Manufacturing enterprises looking to embrace the edge should seek out such highly connected edge infrastructure platforms. Edge data centres need to be in a spread of strategic locations with low-latency connections to diverse connectivity-providers and the main cloud hubs. This connectivity with the public cloud has to be flexible (with the ability to switch cloud connections) and resilient, with route diversity.
Having the capacity for all that sensor data is utterly vital – not just for today, but for the future – as volumes expand and processing requirements change. For this reason, organisations also need edge providers to offer them effective, next-gen cloud tools to manage all their environments. It is inevitable that most manufacturers will continue to operate hybrid architectures, using on-premises environments as well as multiple clouds for various workloads, as appropriate.
“Yet this can easily become difficult to manage and rack up high costs, even before an organisation adopts edge computing. A manufacturer with edge applications that also needs to reconfigure its workloads or integrate new types of application will find it extremely challenging without edge-enabled management tools providing a single pane of glass on all environments.”
Any final words?
“Security is another consideration that is always raised whenever IoT technologies are under scrutiny. Many of these concerns are allayed by SD-WAN technology, which both optimises and monitors network traffic flows, automating many important tasks such as device configuration and patching. New security approaches are summed up in the acronym SASE, allied to zero-trust technologies that also shut the doors on hackers and cyber-criminals.
“There can surely be no debate that the future of manufacturing is at the edge. The time has come for the sector to overcome its lack of knowledge about the relationships between 5G and edge computing, seeking out providers with the insight and experience to know what works best. With the right edge infrastructure partner, manufacturing organisations can transform their operations and create new products, services and business models.”
- The University Manufacturing Circuit Boards from LeavesSustainability & ESG
- Schneider Electric's Commitment to Sustainable ManufacturingSustainability & ESG
- Lenovo & Saudi Alat Building Green Manufacturing FacilitySustainability & ESG
- Nissan Brings Biodiversity to the Factory through RewildingSustainability & ESG