Critical elements to consider in the smart factory evolution
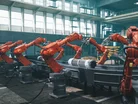
When it comes to breakthrough technological advancements, everyone is talking about language generating AI platforms like ChatGPT. When ChatGPT was first launched as a prototype to the public in November 2022, it quickly grew to over 100m users by January 2023, making it the most rapidly adopted piece of software ever made.
Though many are divided on how this technology should be used and the risks it poses, Hooi Tan, President of Global Operations and Supply Chain at Flex, believes that we can all agree on one thing – this is the kind of technology that will permanently transform the way we live and work.
“In the manufacturing industry, we’re seeing a parallel transformation through the adoption of advanced manufacturing technology. Francisco Betti, Head of the Platform for Shaping the Future of Advanced Manufacturing and Production at the World Economic Forum agrees, stating: ‘For modern manufacturing to truly be innovative, we need to boost productivity and economic growth, while still delivering value to workers, society and the environment at large.’ Having worked at Flex for over two decades, I have seen firsthand the technological forces transforming our industry. I believe that three capabilities will define the next era of manufacturing: real-time decision-making, real-time modifications and smart factory lines.”
Here, Tan tells us more.
How does machine connectivity work?
“A precursor to machine connectivity is ensuring that operations are stable. This means that you have confirmed that the fundamentals of standard manufacturing processes are working and can be executed repeatedly. Once this is in place, you can look at how machines connect with one another.
“The machines in a factory – and going beyond that to include machines in factories in different locations – need to be able to collect data from their environment, analyse it and connect with other machines to share that data and turn it into actionable information and insights. Many machines can be retrofitted to digitise their data with sensors, avoiding massive capital expenditure on new machines.
“In addition to collecting data from machines, you can also collect data from people and processes, varying from numerical and video data to sensors and shift times of line operators. Much of this data is already being collected, but what many companies need to invest in is building out AI models to make better, real-time decisions with the data they have.
“Think of machine connectivity as a nervous system. Nerves extend to all parts of the body (in this case, every aspect of your manufacturing operations) and transmit signals back and forth. The different machines represent body parts – such as the eyes, mouth, ears, or hands – but if the nerves stop transmitting data to the brain (or to your factory’s digital backbone), then that data will not be analysed properly or acted upon in real-time
“For example, injection moulding machines require a lot of maintenance, which can result in downtime. By placing a vibration sensor on the machine, an AI model is constantly fed with vibration data. When there’s a shift in vibration, the model can deduce that the machine needs maintenance or a repair before production is impacted.”
Tell us about making decisions in real-time to optimise operations.
“The good news is that when machine connectivity exists and is functioning properly, it allows for real-time decision-making rather than suffering the consequences of avoidable downtime. In order to set up properly, you need to ensure clarity with an end goal in mind. Here are some questions that you should be asking yourself at this stage:
What decisions need to be made and at what frequency?
“Things to consider: Frequency of decisions can vary widely – anywhere from every 15 days when predicting maintenance for an injection moulding machine to every second for a highly automated healthcare production line to ensure that components are properly connected.
What should our KPIs be?
“Things to consider: KPIs should be based on what you are trying to measure. For example, if you are testing the heat performance of chipsets, numerical KPIs can be used. But if you are measuring something on the move, video KPIs that measure movement or dynamic visualisation would be more appropriate.
How will we track them and adjust?
“Things to consider: With so much upstream data, AI models can indicate that something is going to happen before it does, allowing us to more carefully manage the outcome and stop failures from happening. In the example of the highly automated healthcare product that is produced every second, connectivity must be fast enough to take action in the milliseconds to stop a faulty product from coming off the line.
“Consider technologies that monitor machine performance and can alert when there is a problem with a machine or maintenance required, empowering factory workers to step in and deploy strategies to either avoid downtime or minimise it.
“In this case, being able to make informed, data-driven decisions in real-time can lead to huge cost savings. In fact, a recent report from Deloitte estimated that unplanned downtime costs manufacturers US$50bn each year. In other cases, machines might alert workers when there is a defect in the product or when factory lines are performing below utilisation, which means that a human can step in to make decisions that lead to improved quality or efficiency.
“At Flex, we experience this type of machine-to-machine connectivity every day, managed by our global workforce of 170,000 people in 30 countries. While not every factory is 100% connected to its peers today, we are increasingly building interconnectivity into our entire manufacturing ecosystem, resulting in increased data flow and better manufacturing and supply chain decisions.”
How do you adjust in real-time?
“Beyond arming workers with the information needed to make smart, timely decisions, it’s also crucial that manufacturers invest in technologies that enable real-time modification. For example, at Flex we have deployed IIoT and AI/ML to eliminate bottlenecks in the PCBA testing process.
“For one of our customers, the PCBA end of line functional test had four sections, with one section comprising over 50 steps and lasting more than two hours. If a test failed, the product had to be sent back to the factory floor for debugging before undergoing the entire testing process again. Failing late in the process added significant manufacturing time and created bottlenecks in throughput. To make the testing process more efficient and reliable, we parsed the historical data from each of the test steps and leveraged an AI/ML classification model, to develop an innovative way to reorder and prioritise test steps for maximum efficiency. We saw a 30% overall reduction in test time and a 50% reduction of test time in the case of failures.
“We have also used AI/ML technology to improve the quality inspection process. On one manufacturing line we used vision data in an AI model to ensure each component was placed properly. In this case there were two almost identical capacitors, just with different values, which made it easy for the human eye to make a mistake. Using AI and video, we are able to see if an operator placed the components in the correct spot and in real-time provide feedback to fix any issues. This resulted in greater performance and yield while enabling us to reduce scrap by identifying key issues before a part was sent to another step in the line.”
Tell us about the promise of smart factory lines.
“With machine connectivity and AI/ML, along with other Industry 4.0 technologies, comes the opportunity to optimise and build smart factories. Imagine a factory line where a faulty machine is causing defects in products coming down the factory line. Instead of waiting until the inspection process to discover these defects – at which point, all the products will have to either be discarded or reworked – sensors might recognise the defect the first time it appears.
“At that point, an alert can be sent in real-time, and through AI/ML, the factory line can be stopped, recalibrated, and continued once the issue is resolved. This will make the manufacturing process smarter, more efficient, and more sustainable over time. In allowing AI/ML to make lower-level decisions, we will be able to free up human workers to use their expertise and critical thinking to handle more complex or challenging scenarios.
“We are working on building smarter factories at Flex and are energised by the progress we’ve seen at many of our sites, including GLN factories Althofen and Sorocaba. Our Sorocaba site, which is the first factory in Latin America to receive recognition as a Sustainability Lighthouse, underwent a digital transformation journey that resulted in real-time data and insights that have supported a circular economy ecosystem and better sustainability outcomes, including a 94% reduction of material waste and a 41% reduction in Scopes 1 and 2 greenhouse gas emissions. The site’s cloud-based reverse logistics system used automated materials separation and IoT-enabled collection bins to transform electronic waste and reintroduce materials into the supply chain by repairing, harvesting and recycling parts and materials. In addition to circular economy solutions, the site was also able to reduce energy usage, water consumption and Scope 1, 2 and 3 greenhouse gas emissions with Industry 4.0 technologies like smart utilities management and a digitised CO2 emissions dashboard.”
How are you paving the path forward?
“To help our employees grow and develop the skills needed to succeed, we have training initiatives at many of our sites in conjunction with local trade colleges to reskill and upskill our talent. We also have our global Capability Acceleration Program, which trains employees on a broad range of disciplines including AR/VR, AI, and data analytics to help empower them to succeed in an Industry 4.0 manufacturing environment.
“As we move forward, we must consider the bigger picture, learn from mistakes along the way, and apply our learnings across the entire ecosystem of our manufacturing operations. To reap the benefits of technologies like AI, companies must address it from an enterprise level to holistically determine which areas of the business can benefit from its use, standardise on vendors and usage, and include all stakeholders like IT for data and security.
“Like ChatGPT and other AI platforms poised to have an enormous transformative impact on our world, Industry 4.0 technologies are transforming our industry by connecting manufacturing operations so that machines, processes, and people can continuously learn and make faster, more informed decisions over time.”
*************************************************
For more insights into Manufacturing - check out the latest edition of Manufacturing Magazine and be sure to follow us on LinkedIn & Twitter.
Other magazines that may be of interest - Healthcare Digital.
*********************************************
BizClik is a global provider of B2B digital media platforms that cover 'Executive Communities' for CEO's, CFO's, CMO's, Sustainability Leaders, Procurement & Supply Chain Leaders, Technology & AI Leaders, Cyber Leaders, FinTech & InsurTech Leaders as well as covering industries such as Manufacturing, Mining, Energy, EV, Construction, Healthcare + Food & Drink.
BizClik, based in London, Dubai & New York offers services such as Content Creation, Advertising & Sponsorship Solutions, Webinars & Events.
- Digitalisation as a Strategy to Attract and Retain WorkersDigital Factory
- UPDATED VENUE & DATE – Manufacturing LIVE Chicago 2025Sustainability & ESG
- ABB Cuts Industrial E-Waste in Quest for CircularitySustainability & ESG
- Why Are Manufacturers Doubling Down On Digital Twins?Digital Factory