Digital manufacturing & the Fourth Industrial Revolution
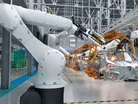
The Fourth Industrial Revolution, otherwise known as Industry 4.0, is characterised by advanced, real-time data and analytics, improved AI and machine learning technology, and greater digitisation and end-to-end connectivity. Over the past few years, the ongoing Fourth Industrial Revolution has transformed countless industries. From the technology and processes implemented, to the way businesses leaders operate and make decisions – its positive effects have been felt far and wide. A crowning achievement of Industry 4.0 has been the ability to take data and insights that were always there and use technology to gather, organise, interpret and act on them. Here, Richard Barnett, CMO at software development company Supplyframe tells us more.
IoT at the forefront of Industry 4.0
One of the signature innovations of Industry 4.0 is IoT.
“It would be an understatement to say that this technology is transforming industrial manufacturing – it is completely revolutionising it by enabling unprecedented connectivity and visibility throughout the production process,” says Barnett. “Sensors and network connectivity on factory machinery are enabling real-time data and updates at every stage. Then, analytics and machine learning can interpret, analyse and communicate the insights into convenient findings for manufacturers. From predictive machine maintenance to supply chain management and inventory tracking, IoT brings a more holistic, data-driven approach to every aspect of manufacturing.”
These insights inform better solutions for industrial equipment manufacturers. For instance, through utilising insights about the manufacturing process, digital manufacturing has streamlined product design.
“Leveraging 3D visualisations, simulations, analytics, and greater connectivity between the various stages in production, manufacturers can anticipate and avoid complications and optimise for efficiency,” says Barnett. “Furthermore, manufacturers are also incorporating virtual reality (VR) for a multitude of purposes, from improving worker safety and training, to factory floor planning and equipment testing, and even product design.”
Finally, IoT distils hundreds of data points down to the essential information that leaders need to make decisions for their businesses.
“This creates digital threads that better connect the real world and digital world, enabling greater visibility as sourcing and production processes move forward,” Barnett continues. “At a time when industrial manufacturers are embracing add-on services as a means of differentiating themselves from competitors, businesses can use IoT and advanced analytics to gain a better understanding of customer behaviour and anticipate changes in demand. Such as, the ability to proactively identify and anticipate changes in demand, lead times, cost and availability and raw materials - not only to secure supply but to negotiate the best cost possible from suppliers and avoid expensive spot buys.”
Richard Barnett, CMO at software development company Supplyframe
AI: Time, money and productivity
Industry 4.0 has provided the technological tools to implement new manufacturing processes that increase output while reducing costs and production times.
“Two technologies that quickly come to mind which manufacturers are embracing are advanced robots and additive manufacturing,” Barnett says. “Integrating advanced robots has bolstered efficiency, as they can be programmed to work unaided around the clock while quickly completing repetitive tasks with accuracy. New robots also possess AI capabilities, allowing for greater flexibility as they can be reprogrammed to accommodate design and production changes. What’s more, they free up employees’ time to focus on the safer and more strategic and analytical tasks – improving working conditions and boosting productivity.”
Meanwhile, additive manufacturing relies on technologies such as 3D printing to build products layer by layer. This method lowers costs, production times, reduces waste, while also simplifying manufacturing to essentially a one-step process. Together, these technologies are helping businesses save time and money throughout the manufacturing process.
“When looking at the gains across a factory network, Mckinsey & Company have reported that it is not unusual to see 30 to 50% reductions in machine downtime, 10 to 30% increases in throughput, 15 to 30% improvements in productivity, and 85% more accurate forecasting. These are impressive returns, therefore it’s no surprise that manufacturing leaders are considering how they can implement and get the most out of available solutions.”
Opportunities for the future of manufacturing with Industry 4.0
The industrial manufacturing landscape is changing rapidly as more businesses implement the new technologies of Industry 4.0. This is only the beginning, according to Barnett.
“Emerging innovations like cloud and edge computing, digital twins, and blockchain will continue to reshape the industry in the years ahead. Leaders face the reality and challenges of today’s supply chains but must also maintain momentum to keep up with these cutting-edge developments. Those that fall behind or fail to embrace the change could struggle to remain competitive in an already tough environment.
“Leaders need to consider Industry 4.0 as a core focal point of a digital transformation in the next five to ten years, with the goal being to create a cohesive vision and holistic strategy that adds value across a manufacturing network. Specifically a combination of connectivity, data visualisation (intelligence and analytics), human-machine interaction, and sustainability. The forward-facing view is that scaling digital transformation requires us to slow down so we can accelerate faster. Those seeking a competitive edge should consider the digital thread across their entire network, and seek out ways to influence multiple steps of that process.”
- The University Manufacturing Circuit Boards from LeavesSustainability & ESG
- Schneider Electric's Commitment to Sustainable ManufacturingSustainability & ESG
- Lenovo & Saudi Alat Building Green Manufacturing FacilitySustainability & ESG
- Nissan Brings Biodiversity to the Factory through RewildingSustainability & ESG