eMobility on the new competitive edge for EV manufacturers
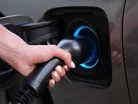
Tesla’s massive investment in battery “gigafactories” and Volkswagen’s plan to build six dedicated battery production plants in Europe by 2030 indicate that the battery has become the most strategically important component in the automotive industry.
Paul Hartanto-Doeser, eMobility System Technologist at Analog Devices
EV batteries and car manufacturing
Car manufacturers’ efforts to reduce the size, weight, and cost impacts of batteries over a vehicle’s complete life cycle, and to extend the driving range that the battery supports, will have a huge impact on their market share and competitiveness. As increasing numbers of older EVs reach the end of their life, car manufacturers will be competing for the value derived from so-called second life batteries recovered from scrapped vehicles.
The news headlines about battery developments tend to highlight research into the new and sometimes exotic materials that might one day be able to store more charge than today’s lithium technology; a completely different part of the battery - the battery management system (BMS), which monitors the state of charge (SOC) and state of health (SOH) of the battery—tends to go under the radar. However, a new wireless battery management system (wBMS) technology—developed by Analog Devices and pioneered by General Motors in its modular Ultium batteries—promises to give car manufacturers a new competitive edge across the whole of a battery’s life, starting from when battery modules are first assembled, to operation in an EV, beyond to disposal, and even into the battery’s second life.
Norbert Bieler, eMobility Director Business Development at Analog Devices
The cost, space, weight, and design problems associated with wired connections in the EV battery
In a conventional EV battery, wiring supports communication between each cell in the battery pack and an electronic control unit (ECU), which regulates its operation to ensure that it provides power to the vehicle.
This requirement for communications inside the battery reflects the complex architecture of a large battery pack: it is made up of modules, each of which contains multiple cells. Natural production variations mean that each cell has individual characteristics that vary within a specified tolerance range. To maximise battery capacity, lifetime, and performance, the key parameters of battery operation—voltage, charge/discharge current, and temperature—need to be monitored and logged individually for each module. This is the job of the cell monitoring units in the BMS.
But the data from each cell only become useful when they reach the BMS’s ECU, which controls the way power is supplied to and drawn from the battery, module by module, and maintains the battery’s safety functions.
This is why an EV’s battery requires a means to transfer data from each module—where voltage, current, and temperature are measured—to the ECU’s processor. Traditionally these connections have been made with wires: wired connections have the advantage of being familiar and well understood.
It is not difficult to compile a long list of disadvantages: a copper wiring harness is heavy, and occupies space that, if filled by a battery cell, would give extra energy capacity. Additionally, the connectors can potentially suffer from mechanical failure. In other words, wires increase development effort, manufacturing cost, and weight, while also reducing mechanical reliability and usable space. This results in reduced driving range. Get rid of the wiring harness, and the car manufacturer also gains new flexibility to design the form factor of the battery pack to fit the design requirements of the vehicle.
The complexity of a battery’s wiring harness also makes the assembly of a battery pack difficult and expensive: wired packs must be assembled, and the connections terminated manually. This is a costly and hazardous process because high voltage EV battery modules are supplied charged. To maintain the safety of the assembly process and to protect production line workers, rigorous safety protocols are applied.
In GM’s implementation of the wBMS technology, the scalable architecture of the Ultium modules also helps lower the cost of the battery pack to GM. While the Ultium battery had its debut appearance in 2021, the modules will be deployed across the range of GM vehicles, not only in heavy duty vehicles but also in all road cars, from performance and premium cars to small vehicles. As Kent Helfrich, GM executive director of Global Electrification and Battery Systems, mentioned in a September 2020 press announcement, “Scalability and complexity reduction are a theme with our Ultium batteries—the wireless management system is the critical enabler of this amazing flexibility.”
The wBMS technology makes it easy to read out critical battery data from each intelligent module: this means that the condition of each battery module can be determined individually and wireless. This data can, for instance, provide information about the SOC and SOH of a module without connecting via cables to a test station. In combination with data from when the module was originally produced, this allows the optimal usage of second life modules in their next application, and the provision of a detailed set of specifications for each module on sale. The data’s ready availability increases the resale value of the modules.
- The University Manufacturing Circuit Boards from LeavesSustainability & ESG
- Schneider Electric's Commitment to Sustainable ManufacturingSustainability & ESG
- Lenovo & Saudi Alat Building Green Manufacturing FacilitySustainability & ESG
- Nissan Brings Biodiversity to the Factory through RewildingSustainability & ESG