FANUC/Rockwell Automation address manufacturing skills gap
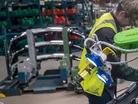
To address the manufacturing skills gap, FANUC America and Rockwell Automation have formed a coalition to accelerate work and learn apprenticeship programs to upskill current and future workers for jobs in advanced manufacturing, robotics and automation.
“As industry adopts new technologies, it is vital to be able to quickly adapt with a well-trained workforce. Having the most current standards will drive manufacturing competitiveness and simultaneously grow new talent to these new occupations, upskill current employees, and allow companies to be more agile in their workforce planning,” said Michael Cook, Director Global Academic Organization, Rockwell Automation.
The Coalition: addressing the skills gap
As part of the coalition, APT - a FANUC and Rockwell Automation systems integrator - and NOCTI Business Solutions, which provides independent assessments of occupational standards and validation using recognised ISO, will be used.
In addition, Franklin Apprenticeships - a key partner of the coalition - will ensure there is an apprenticeship support structure, as well as success enablers for employers and apprentices.
The coalition has developed new programs providing opportunities for apprentices to gain credentials that include fundamental robotics (Robot Operator) and automation (PLC Operator), as well as further higher levels for Robot and PLC Technicians and Integration Specialist builds.
It is expected that all new offerings will provide more people with fulfilling careers and help companies to bridge the demand for skilled workers.
“Our number one goal is to help create a worker pipeline that will not only help people increase their skills and future earning potential, but to help manufacturers achieve their production goals and maintain a thriving economy. In most cases, current and future workers can complete the apprenticeship skills training and achieve their industry-recognized certifications in less than one year. It’s also important to note that these programs support all types of apprenticeship and certification models, including pre-apprenticeships,” commented Paul Aiello, Director of Education, FANUC America.
“As technology advances at a fast pace, it is important that companies play a bigger role in education to ensure a safe, productive and sustainable work environment. FANUC and our coalition look forward to helping as many people as possible take advantage of these accelerated work and apprenticeship programs,” concluded Aiello.
For more information on manufacturing topics - please take a look at the latest edition of Manufacturing Global.
- The University Manufacturing Circuit Boards from LeavesSustainability & ESG
- Schneider Electric's Commitment to Sustainable ManufacturingSustainability & ESG
- Lenovo & Saudi Alat Building Green Manufacturing FacilitySustainability & ESG
- Manufacturing & Mobility LIVE: Neby Ejigu, FINN PartnersTechnology