Ford: unlocking 5G potential for electric vehicle production
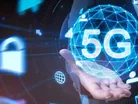
In a recent announcement made by Ford , the automotive organisation and its consortium of partners have received government backing to introduce 5G connectivity within its manufacturing to speed up the production of electrical vehicles.
Delivered by Vodafone Business, the 5G mobile private network will be install this year in the companies Electrified Powertrain in Manufacturing Engineering (E:PriME) facility on Ford’s Dunton Campus
“Connecting today’s shop floor requires significant time and investment. Present technology can be the limiting factor in reconfiguring and deploying next-gen manufacturing systems. 5G presents the opportunity to transform the speed of launch and flexibility of present manufacturing facilities, moving us towards tomorrow’s plants connected to remote expert support and artificial intelligence,” commented Chris White, Ford’s 5GEM project lead.
The Vodafone Business 5G solution is said to be able to overcome many of the issues relating to wireless connectivity in the industrial industry, by reducing delays, providing a wider bandwidth, improving security and reliability and increasing deployment times.
“5G mobile private networks act as a springboard for organisations, allowing them to rethink the way they do business. In this case, MPN technology makes the factory of the future possible. It allows machines and computing power to coordinate in real time, improving precision, efficiency and safety. We’re excited to help Ford plan for the future of its business,” Vinod Kumar, CEO of Vodafone Business.
Once complete, Ford will have the fastest possible connectivity, as well as the consortium’s second network welding research specialists TWI, based in Cambridge. The connected equipment at both sites will provide Ford with real time control and analysis, as well as expert support to ensure that new manufacturing processes are ready for the shop floor.
With these capabilities provided by Vodafone, Ford will focus on the connectivity of the welding machines when manufacturing electric vehicles. Currently for the batteries and electric motors in an electric vehicle, requires 1,000 welds, for a single product, Ford explains that this could generate more than half a million pieces of data every minute.
“Fast, reliable, high capacity data capture and analysis will be a significant requirement of these processes. Connecting the data with experts, such as TWI and manufacturers, is critical if processes are to develop at the same rate as these innovative products demand,” said Ford in a company statement.
“We’re determined to harness this revolutionary technology to boost the productivity and growth of UK industries. We want Britain to be a world leader in 5G, and since 2017 the government has invested millions in ground-breaking testbeds and trials across the country to achieve this,” Oliver Dowden, Secretary of State for Digital, Culture, Media and Sport.
For more information on business topics in Europe, Middle East and Africa please take a look at the latest edition of Business Chief EMEA.