The importance of agile design in the automotive industry
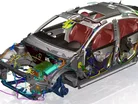
The automotive sector is one the world’s most important industries. It spends over £66 billion annually on research and development, it employs around 12.9 million people in Europe and, at over £1.3 trillion a year, its value is surpassed by only four economies.
Despite its success, the sector faces challenges. Consumer behaviour is leading to demands for connected, smart and autonomous vehicles. A modern car is a high-tech machine and automotive companies are busy trying to reinvent our driving experience.
Software will only continue to grow in importance as we progress to fully autonomous vehicles. Indeed, it’s a key reason why car design is becoming so much more complex than it was before.
The tech arms race
The automotive industry finds itself in a race to develop smarter and, ultimately, autonomous vehicles. Indeed, it’s a key reason why car design is becoming so much more complex than it was before.
New ways of working needed
As more next generation vehicles hit the roads, it is a reminder that car companies must simplify vehicle development processes and shorten development cycles by prototyping in more agile and efficient ways.
This agility can be achieved by creating digital clones of new models. These models enable much of the development and testing to take place in the virtual world and thereby accelerating the design, test and approve cycle.
To move to a digital design environment, we recommend five steps:
Creating the digital twin of the car is only the first step. To achieve the best product development, it is important to create a digital enterprise designed to foster innovation.
More clean-sheet design
Clean-sheet design is an approach used widely in aerospace. The aerospace companies host projects, teams and suppliers on a modular but integrated set of tools to reinvent every aspect of the plane. While particular softwares are used extensively in the auto industry, we believe that the scope and capabilities of these need to change. The reason for this is that, with every area of design being scrutinised, it’s essential to coordinate change between different functional areas to ease complexity. Tools must make it easier to unite development packages in a single product design and simulation environment; create and update technical documentation; configure and manage bills of materials; and coordinate people and processes towards shared goals.
The software era
We’re progressing towards fully autonomous vehicles and, as we move down that path, the million or so lines of software code we have now will explode. Safety is an especially interesting area. From the alert and lane crossing systems we have today, we’re moving towards more advanced driver observation applications. For example, wearable technology can link to the car’s system to observe stress and tiredness levels, with the vehicle taking over more tasks – including driving if the driver’s awareness is becoming compromised. In addition, in the event of a crash, sensors will communicate the location, severity and possible injuries of occupants to blue light services. This is complex automation and writing, testing, amending and monitoring software code is a time-intensive task that must be simplified to help ease change management and compress development cycles.
Integrate Computer Aided Engineering and Computer Aided Design (CAD): We are seeing increasing need to align design and engineering analysis activities along with integrating this with vehicle testing and simulation. By using 1D and 3D digital models in vehicle prototyping time can be significantly reduced because it’s impossible to physically validate all the components, designs and parts when design validation happens in an iterative way. By integrating the virtual and physical world, we can understand component performance prior to signing-off on fabrication to help cut product development costs and timelines.
Model the software: Given the importance of software in automotive, it’s imperative to make it much easier to create, document, store and run tests on codes. An integrated software environment makes it easier to develop and manage embedded software from project inception to end-of-life and make this process integral to the overall vehicle development plan. This enables management of large-scale software deployments while ensuring traceability and error checking.
Execute change: With the massive amount of change requests that happen in a global program launch, it’s vital to better connect engineering and manufacturing systems.
Engineering and manufacturing must work together to determine what type of tooling and operations changes are required to handle different vehicle configurations. A digital project management platform makes it easier to combine product engineering, manufacturing engineering and shop floor execution into integrated systems. The visibility and control provided by uniting these capabilities in one interface helps cut complexity to get to market faster and ensure that, when the product is launched, the right processes – and process controls – are in place.
Complexity and control
There’s no doubt that automotive design and production is becoming much more complex. And while technology, in the form of complicated software interactions, is a root cause of this challenge, it has the potential to provide the answer.
A cohesive suite of tools across design, testing, simulation, production and execution analytics, means it’s much easier to manage virtual teams, contain costs, and automate and validate development processes.
As the industry enters a period of intense investment and competition, the likes of which we have not seen before, smart innovation portfolios can help automotive teams design, engineer, manufacture, and most importantly, achieve innovation.
Kirk Gutmann is the SVP of industry strategy at Siemens PLM Software
- Smurfit Kappa collaborates with artist Oliver Grossetête to produce corrugated boxes into artAI & Automation
- Ball Corporation wins silver and bronze awards for design innovationLean Manufacturing
- What does generative design and AI mean for design thinking?Technology
- How virtual reality can improve design engineeringTechnology