Making Britain's manufacturing smarter: Expectations for 2018
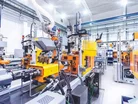
First came the dawn of mechanical machines, succeeded by the introduction of electricity, quickly followed by the third industrial era, the advent of computers and the internet. Now, as we enter the so-called fourth industrial revolution, Industry 4.0 is moving from buzzword to reality. In this article, Martyn Williams, managing director of industrial software provider, COPA-DATA UK, examines what is needed to achieve Britain’s goal of becoming an Industry 4.0 leader in 2018.
Rising adoption of industrial technology
In 2018, the manufacturing industry will see a higher adoption of industrial digital technologies (IDTs) — think robotics, intelligent automation software and additive manufacturing. These technologies have been available for a while, but greater accessibility means they are no longer out-of-reach for small to medium-sized manufacturers.
According to the Annual Manufacturing Report 2017, the majority of manufacturers believe that increased connectivity in their facilities will help to increase their productivity. However, the benefits of IDTs are even greater when replicated on a national scale. Increasing Britain’s output will assist in the country’s worldwide competitiveness, strengthening supply chains and, ultimately, strengthening the UK as a world leader in industrial digitalisation.
Investments for innovation
The country’s engineering skills shortage has been a hot topic of conversation for a while, but only recently is the industry recognising the importance of increasing innovation — rather than just high investment. One of the recommendations of the Government’s review on industrial digitisation, Made Smarter, is to create a national Skills Strategy to identify the skills requirements in the UK. However, this will only work in tandem with investments that will encourage innovative behaviour.
By nature, engineers want to design, invent and create things. The increase in digitalisation on the factory floor has been widely criticized for removing the need for human intervention and, therefore, removing the need for highly-skilled engineers — but this view is misguided.
Digitalisation provides an opportunity for engineers to move away from the menial, repetitive jobs that automation can manage. Instead, engineers must begin to use their expertise and talent for defining and leading the strategies and processes needed for such a high level of automation.
Inspiring stronger leadership
For Britain to become a pioneer of industrial technologies, the country needs inspiring leadership, but management is not just about maintaining authority. Positive leadership requires a divestment of power by giving employees the authority to make decisions.
Consider this. A machine operator in a factory is arguably the best qualified person to make decisions about a particular piece of equipment. Despite this, the decision to repair or replace a machine is often passed to C-level. Our worldview limits the way we think and skews our understanding of the wider picture. But, to make the best decisions, the authority must be shared with those that are most informed.
It is our responsibility to create the next generation of leaders — these are our apprentices, graduates and machine operators. However, as Britain’s industrial landscape is changing so quickly, we cannot simply create replications of ourselves. As the factory of the future continues to adapt, our future leaders need get used to taking ownership of important business decisions.
To become a pioneer of industrial digitalisation, Britain’s manufacturers need to invest in technology, encourage innovation and inspire the next generation. Britain may have been the first country to industrialise during the early 19th century, but, today, it has the potential to become a global leader of the next industrial era.