P2i: Mitigating the Risk of Electronics Liquid Damage
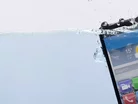
The worldwide IoT devices market has grown exponentially in recent years, with the number of devices projected to grow to 25.44 billion in 2030, up from 7.74 billion in 2019. The increasing availability and affordability of daily-use electronics is however raising the risk of liquid damage taking place, and it’s not just the typical splashes or spills from an accident with the morning coffee that pose a risk. Humidity and accidental submersion need to be considered, particularly as a study by P2i found that 50% of research and development professionals identified accidental submersion as a risk factor. Another emerging trend has been for devices to be cleaned more regularly in recent years.
Scoping the liquid protection challenge
Many device users are potentially unaware of the range of liquid products that can cause lasting damage. With consumers now more concerned about maintaining hygiene with increased awareness during the Covid-19 pandemic, the primary reason given in P2i’s study for devices needing better liquid protection in the modern area was the increased incidence of consumer cleaning with antibacterial products. This trend looks set to stay. Nearly half (44%) of respondents surveyed reported that the pandemic will have a long-term impact on liquid protection in the design requirements of electronic devices due to the increased cleaning taking place. With these risk factors at play, it’s important to delve into the science behind liquid damage.
The science behind liquid damage
The fast pace of modern life means that accidents frequently happen, and electronic devices are regularly at risk of contact with liquids. Additionally, devices are now more frequently exposed to liquids intentionally and need to be protected sufficiently. When an electronic device comes into contact with a liquid through gaps or openings, the residual liquid is left on internal components. The device is then at increased risk of short-circuiting and internal corrosion follows, ultimately leading the consumer to dispose of the device.
A United Nations survey in 2020 found that a record 53.6 million metric tonnes of electronic waste was generated worldwide in 2019, an increase of 21% in just five years. Mitigating these rising levels will help play a vital role in tackling climate change, and sufficient liquid protection can help this to be achieved. 95% of respondents in the P2i survey confirmed that a product without liquid protection would fail within the first two years, adding to the increasing levels of e-waste.
How manufacturers can take action
It’s clear that liquid protection is needed for devices, but which solution should manufacturers turn to? There are several options for those looking to secure electronic devices:
Conformal coatings – This is where a thin polymeric film is applied to a circuit board’s components which conforms to the contours on a printed circuit board. The main disadvantage of this method however is that it is applied in a liquid state and then cured by thermal or UV curing. This can result in a wide variation in thickness, adherence and quality, affecting reliability. Longevity compared to other solutions is also an issue. Because of these inherent drawbacks, it’s unlikely they will be selected for safety-critical components.
Mechanical seals – In a similar sense to conformal coatings, mechanical seals are a traditional method to apply liquid protection to devices and these work via sealing the point of entry where liquid could enter the device. This method however adds weight and bulk to devices, and risks degradation in everyday use, leading to loss of effectiveness. They also trap heat around microprocessors and operating components, which require cooling to ensure optimum function. Mechanical seals also struggle to retain their position of use, leading to moisture and liquid ingress and corrosion damage.
Nano-coatings - Nano-coatings are repellent coatings applied to the product in the gas phase at low pressure. These penetrate complex 3D structures and bond at the molecular level to both the external and internal surfaces of an electronic device. By adopting this approach, manufacturers can ensure that devices repel water attempting to enter from outside the device, but can also prevent liquids from reacting with the critical internal electronic components, meaning the risk of corrosion is drastically reduced; if not eliminated.
Nano-coatings provide the solution
Such is the increasing popularity of nano-coatings that P2i’s survey of research and development professionals discovered that 61% said they use a variation of nano-coatings as part of their overall liquid protection solution. Nano-coatings also provide longevity, a particular downside with conformal coating or mechanical seal options. This was reflected in P2i’s survey, which found that 53% of respondents felt that one of the main advantages of the technology was long-lasting liquid protection.
For manufacturers, the numerous benefits of nano-coatings make them the perfect solution for effective liquid protection for devices. The longer-lasting protection ensures that a product’s life can be extended and kept in use by a customer for a longer period of time, reducing levels of damaging e-waste. For manufacturers, longer product life can enable them to achieve cost savings from fewer repairs needing to be made. The result for manufacturers is an upheld brand reputation through the creation of reliable products that meet the market requirement for sustainable products.