Top 10 digital factories: BMW
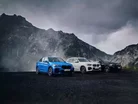
Featuring in our Top 10 digital factories, we look at how BMW Group is adopting industry 4.0 solutions to digitalise production.
Opening up a world of opportunities for BMW Group, Industry 4.0 within its production system enables “fulfilment of individual customer wishes and enhances the flexibility and quality of production processes.”
The group is driving modernisation within its production by digitalising its systems via four key technology clusters: smart data analytics; smart logistics; innovative automation and assistance systems and additive manufacturing.
This digitalisation and innovation is impacting the entire BMW Group production value chain. “From press shop to body shop to paint shop, from assembly to logistics – every stage of production benefits from the use of digital processes,” comments BMW Group.
Smart data analytics
Smart data analytics - the capability to capture and evaluate data to improve processes. BMW Group harnesses this technology in a number of ways including:
-
Algorithm analysis of thousands of bolted connections in when a vehicle is assembled providing an important input for more reliable identification of errors before they occur.
-
Harnessing the capability of virtual reality, creating a 3D environment in real-time. The virtual spaces and scenarios are used to optimise processes and safety.
-
Utilising intelligent data analysis to help improve quality across the entire value chain. With this analysis of data, the group can expand process specifications to include a subjective analysis.
Smart logistics
By harnessing smart data technologies and real time information for its entire supply chain, the BMW Group is striving to develop ground-breaknig systems for smarter and more flexible logistics operations.
“The focus is on applications such as logistics robots, autonomous transport systems at plants and digitalisation projects for an end-to-end supply chain,” comments BMW Group.
How BMW Group is harnessing technology within its logistics:
-
Autonomous tugger trains: used in assembly logistics, these robots use laser signals to navigate independently through production halls.
-
Smart transport robots: these robots are able to transport components weighing up to 0.5 tons independently. The technology uses wireless transmitters to determine their location, and can calculate the best route to the desired destination. These transport robots are also powered by recycled BMW i3 batteries with a capacity to drive for eight hours.
-
Connected distribution: via the group connected distribution network, vehicles send and receive information relating to their route from plant to dealership. When it stops the vehicle relays its geolocation and status to the logistics centre.
Innovative automation
When it comes to innovative automation, BMW Group strives to use intelligent solutions to relieve employees, complementing human flexibility and sensitivity with the strengths of robots.
How BMW Group is harnessing innovative automation:
-
Collaborative lightweight robots: BMW Group's collaborative robots work alongside employees, performing strenuous and high-precision tasks. Its lightweight robots are extremely versatile, however their speed is limited and they can come to a standstill if any dangers arise.
-
Exoskeletons: like a second skeleton, these types of robotics work as an external support for the body, strengthening employee legs, arms or back.
Additive manufacturing
Dating back to 1990, BMW Group has been prototyping additive manufacturing (3D printing), and has continued to develop this technology. With the use of additive manufacturing methods, production times for parts will further shorten, as well as providing greater potential for more economical and flexible production, and individualisation of components.
How BMW Harnesses additive manufacturing methods:
The additive manufacturing centre: located at BMW Group’s research and innovation centre (Munich), the additive manufacturing centre handles almost 25,000 prototype orders, building over 100,000 components a year. Alongside BMW i Ventures, the centre is also investing in start-ups and new companies to develop ground-breaking technologies.
Series components: in 2010, BMW Group completed its first successful use of the technology in a small series production for water pump wheels within its DTM vehicles. Other series components include a 2012 production for plastics parts in Rolls-Royce Motor Cars, and in 2017 for metal parts in the BMW i* Roadster.
Customised assembly aids: BMW Group has not only harnessed this technology for production parts, it has also utilised 3D printing to produce individual thumb supports to relieve employees working in vehicle assembly to avoid excessive strain on the thumb joint.
To find out more about BMW Groups use of industry 4.0 solutions, click here!
SEE ALSO:
For more information on manufacturing topics - please take a look at the latest edition of Manufacturing Global
Follow us on LinkedIn and Twitter
Image source: BMW Group