Why Stora Enso's new dry Forming Production Unit Matters
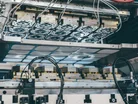
Established in Helsinki in 1998, Stora Enso has emerged as a key player in the paper and forest product industry.
By embracing wood fibre for packaging solutions and timber for construction projects, its emerged as a key sustainable leader in its manufacturing vertical.
Continuing its dedication to furthering sustainable packaging, Stora Enso has announced the opening of a groundbreaking dry forming production unit in Skene, Sweden.
Why us this unit groundbreaking? Because its the largest and most advanced dry forming production unit in the world, significantly advancing the development of sustainable packaging technology.
The Skene production unit utilises an innovative dry forming process to produce high-performance formed fiber products, such as cup lids, which replace the plastics traditionally used in food and beverage packaging.
Plastics which notoriously pollute the environment.
Any excess material produced during dry forming is reused and recaptured, creating a circular process with minimal wastage.
Unlike conventional wet forming, the dry process reduces water and energy consumption significantly, thus offering an even more sustainable manufacturing method for fibre-based packaging.
This innovation is possible thanks to Pulpac's advanced technology.
The company's Dry Molded Fiber technology provides efficient production at high speeds, which allows Stora Enso to meet rising market demand for fully biodegradable, renewable and recyclable fibre-based packaging solutions.
The products produced with dry forming technology offer a significantly lower CO2 footprint compared to single-use plastics.
The dry forming process offers also flexibility in barrier additives for customized functionality as well as an excellent surface finish with the option to advanced decoration possibilities.
“Stora Enso is the first producer to successfully implement this new dry forming technology on a large scale,” says Anna Stenström, Operations Director at the Skene Production Unit.
“We are truly excited to pioneer this new approach and to explore all the possibilities it offers to shape the future of sustainable packaging.”
“The Skene production unit represents another great advancement in biomaterials by Stora Enso," adds Juuso Konttinen, Senior Vice President of Biomaterials Growth Businesses at Stora Enso.
" The dedication of our team and the collaboration with PulPac and other suppliers has enabled us to scale up this innovative technology to meet the continuously growing demand for high-quality and more sustainable products.”
In addition to Stora Enso's investment in new facilities is the success of its ongoing Beyond Board Packaging Services.
Beyond Board Packaging Services
Stora Enso's Beyond Board Packaging Services provides manufacturers comprehensive sustainability training covering areas such as sales, sourcing, and product management.
Participants gain insights into forestry, fibres, the principles of circularity and recyclability, and packaging’s climate impact.
- Sustainability training
- Regulatory services
- Circularity assessments
- LCA Services
Through this holistic education, Stora Enso helps to enhance awareness and demand for sustainable packaging solutions.
It also highlights that the paper manufacturing industry can protect forests and use them to sustainable advantage.
As Toby Croucher, SVP Forest Sustainability at Stora Enso says: “Humankind can drive sustainable forest management and use wood effectively at the same time – the two are not mutually exclusive!"
Toby goes on to add that this requires a mindful, proactive approach.
" Using wood requires scrutiny, given that harvesting, if not done sustainably, can pose a risk to biodiversity,” he adds.
“But, protecting forests is firstly about being proactive. Our forestry operations are planned according to approved biodiversity management practices which aim to preserve specific structural features throughout the forest’s lifecycle. In addition, we look at all stages, from harvesting to regeneration, using a science-based approach to enhance the biodiversity of our forests.”
Stora Enso continues to drive the development of sustainable packaging solutions.
Tackling unnecessary plastic and paper waste is critical to create a more sustainable world and manufacturing industry.
With efforts like these we all come a step closer.
Make sure you check out the latest edition of Manufacturing Digital and attend the next Manufacturing LIVE event - Manufacturing & Mobility LIVE (virtual)
Also sign up to our global conference series - Procurement & Supply Chain 2024 & Sustainability LIVE 2024
Manufacturing Digital is a BizClik brand.
- Schneider Electric's Commitment to Sustainable ManufacturingSustainability & ESG
- Henkel: Optimising Washing Through Autonomous SensorsSustainability & ESG
- Lenovo & Saudi Alat Building Green Manufacturing FacilitySustainability & ESG
- BMW: Creating Economic Circularity through Battery CreationSustainability & ESG