Manufacturers struggle to keep supply chains resilient - BCG
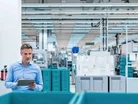
Businesses are struggling with making their supply chain more resilient, say Boston Consulting Group, because many businesses are new to the quest for such resilience.
Jeremy Kay is MD and Partner with Boston Consulting Group, and says that many clients are “expecting things to go wrong in significant ways” and that they recognise the stable supply of goods and materials “as a thing of the past”.
And yet, he says, many struggle to get a handle on how resilient they need to be.
“They don't necessarily know the real value of resilience, and therefore how much they should be willing to invest in resilience,” he says.
“They also don't know how far they need to go to mobilise the organisation. Some companies assign one person, whereas others have set up teams of people dedicated to building operational resilience.”
High inventory stocks don't bring resilience
Kay warns that it's important businesses understand that building up inventory is not a panacea for supply disruption.
He says: “I've recently heard from two clients that their service levels are still lower than before the pandemic, even though their inventories are at an all-time high. “Building inventories has also hurt their cash flow and working capital. The harm to their balance sheets is starting to concern their financial leaders.
“This situation wasn’t as problematic when demand kept rising, but with slower growth and a looming downturn, spending heavily on inventory isn’t sustainable.”
Kay also says businesses can get bogged down in “analysis paralysis” when it comes to resilience strategies.
He says: “We advise clients to focus on investments that will give the best resilience returns, given their risk profile.
“It’s like investing in an insurance policy: you don’t want to pay for more insurance than you need but you don’t want to be underinsured either.
“Striking the right balance for resilience investments is hard but it’s better to make some assumptions and take action than to get stuck in analysis paralysis.”
Manufacturing in Asia a concern for US firms
Kay says that, in North America, the types of disruptions companies most concerned about includes risk around manufacturing and sourcing in Asia.
“North American companies' heavy dependence on Asia makes them highly vulnerable to shortages of global shipping capacity and rising geopolitical tensions,” he explains.
He adds: “We recently helped an electrical-equipment manufacturer assess the health of its supply chain. The most important lens for its leaders was getting a good view of their exposure to Asia.”
Kay says such exposure is especially problematic for products sourced from a single supplier.
“To prioritise the related risks, we distinguished products for which alternative suppliers are readily available versus highly engineered products for which the company must rely on a sole source,” he says.
Kay adds: “For the latter, especially in high-risk cases, the company can try to redesign products to enable sourcing from alternative suppliers. It can also do this proactively for products in development.”
Another option, he says, is for businesses to establish processes that enable quick reactions to disruptions relating to products identified as being at high risk.
Labour issues troubling many firms
Labour is another complicating factor, says Kay.
“Companies are concerned labour shortages are harming their operations, even within North America. Some struggle to find enough people to operate their machines and get products out the door.
“To address these challenges companies recognise that they need to enhance their abilities to quickly identify and assess risks, react fast, and absorb the impacts of disruptions across the supply chain.
“To build this operational resilience, they are investing in tools for real-time monitoring and prediction, broadening design specifications, and building inventories.
“They are also rethinking their labour and automation strategies to avoid getting burned by staffing shortages.
"To shorten supply chains and expand their labour pools, some companies are near-shoring manufacturing operations to alternative locations in North America, such as Mexico.
"To truly become resilient, companies need to build a wide variety of capabilities to, for example, gain visibility, achieve greater flexibility, and react faster to disruptions. Developing only a few of these capabilities is not enough."
- Siemens, Sony & NVIDIA Unveil New Industrial AI Tools at CESAI & Automation
- Manufacturing Unwrapped: Inside IKEA, The Wonderful EverydayProduction & Operations
- Carbmee: Helping Maersk & Coca-Cola Curtail Carbon EmissionsSustainability & ESG
- EY: How Technology Can Power Green ManufacturingSustainability & ESG