Dynabook on hybrid work for European SMB manufacturers
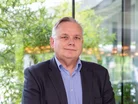
More businesses are looking to perfect their hybrid model to ensure an improved work-life balance for their employees, improve productivity and create better internal relationships.
The manufacturing industry's digital transformation journey has been rapidly accelerated, although when handling back-office and on-site employees, finding the right level of flexibility that’s fair for all can be hard to do.
Hybrid working environments are going to be (or already are) the norm for many industries, with organisations around the world putting more time, effort and money into optimising their strategy. Yet, our latest report showed that only 11% of European SMB manufacturers believe they have sufficient IT resources to support their hybrid workforce.
This is despite nearly half (49%) of SMB manufacturers seeing an increased IT budget this year. Indeed, 75% feel they are yet to ‘fully optimise’ their IT solutions for hybrid working.
There is no “one size fits all” model for hybrid working. Each business requires different measures. However, the numbers above show there’s clearly room for improvement and that many SMB manufacturers still haven’t got the right tech to run efficiently.
How can manufacturers ensure best practices and good equipment management when implementing a hybrid working model?
SMB manufacturing leaders now have the opportunity to be more creative and engage with employees on a higher level to create a more responsible environment.
When working in any team, communication has to be a key priority. In order to create a more stable foundation for hybrid working, ensure that everyone in the team is communicating their preferences around how they want to work and has a clear understanding of their expectations of them.
Furthermore, employees need to understand how they can better discuss IT issues. Encouraging open communication between your employees can also highlight other potential problems especially since not all roles can be entirely remote.
For example, 89% of European SMB manufacturers believe they need a full or partial hardware refresh. By incorporating more transparent communication, employers can proactively look to support workers better and create the best solution(s) for everyone involved.
What are manufacturers’ new IT priorities?
Most manufacturers have clear priorities when it comes to their next IT purchasing decisions. However, it’s clear that certain technologies are considered more important now than they were before the pandemic.
Our research bore this out. SMB manufacturers were asked which technologies are most important for their business when transitioning into a hybrid workspace, and there were three standouts:
- Virtual Desktop Infrastructure (VDI) (55%)
- Laptops (56%)
- Cloud platforms (66%)
Limiting network downtime is the highest priority for almost half of European SMB manufacturers (46%) since any prolonged period can have a tremendous impact on overall operations.
Establishing a secure hybrid work model is a significant challenge for manufacturers. But by utilising the best technology available, companies will only drive better working practices.
What is the role of managed service providers (MSPs)?
To meet the changing requirements of employees many manufacturers are looking to outsource IT and procurement work through managed service providers (MSPs).
MSPs can integrate into your organisation and be readily available to help any manufacturer when faced with IT issues or require upgrades, without the input of any employees. This flexibility is a major plus side to working with MSPs.
However, our research highlights that the cost of engaging with MSPs is a clear hurdle for many European SMB manufacturers, with three-quarters (75%) starting price to be the main reason they avoid working with MSPs.
Given the complex nature of setting up hybrid strategies, the move to managed service offerings creates an increased need for due diligence processes and auditing.
It also demands increased responsibility from service providers - they need to be able to guarantee the protection of their customer's networks and data from cyber threats.
What other concerns do manufacturers have around hybrid working?
Anything considered ‘disruptive’ can be viewed as either a hindrance or an opportunity.
When it comes to hybrid working, it’s important for SMB manufacturers to take the initiative to drive the digital transformation they’re aiming for. Adopting a hybrid working model can vastly improve not only business growth but also reputation and employee relationships.
That said, concerns and issues around cybersecurity, hardware accessibility and costs have meant that only 22% of SMB manufacturers fully agree that they have achieved a hybrid or remote working optimal state at some point during the pandemic.
Without implementing security awareness training, your employees may blindly walk into a security risk when browsing online or if they decide to use an unsecured network.
Creating effective hybrid working collaboration
There’s no doubt that, without a clear strategy, hybrid models can bring a number of new challenges for SMB manufacturers. Often it will ultimately come down to the people that make up your workforce, installing effective leadership and providing the proper resources.
Encouraging collaboration and maintaining strong communication, as well as acquiring the right hybrid working tools for your business, will lead to an improved working environment.
Key Points for Manufacturers When Adopting a Hybrid Working Model
- Put transparency at the heart of all working practices
- There is no such thing as over-communication
- Look to empower employees by allowing input on processes and feedback
- Test different approaches and take learnings from each new initiative
- Make use of the technology available to support hybrid working
- Understand the capacity of your IT team - managed service providers might at first be deemed too costly but they can streamline much of the work
Written by Nick Offin, Head of Sales, Marketing & Operations at Dynabook Northern Europe (formerly Toshiba PC Company)
- The University Manufacturing Circuit Boards from LeavesSustainability & ESG
- Schneider Electric's Commitment to Sustainable ManufacturingSustainability & ESG
- Lenovo & Saudi Alat Building Green Manufacturing FacilitySustainability & ESG
- Nissan Brings Biodiversity to the Factory through RewildingSustainability & ESG