Four ways mobile robots can improve operational safety
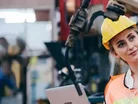
While workplace safety is important for all industries, for those in high risk industries such as manufacturing, warehousing and transportation it is a major concern which has only increased with the impact of COVID-19.
With 72 per cent of manufacturers reporting that collisions and other shop floor accidents are a big challenge for their businesses, the recent statistics from the Bureau of Labor Statistics (BLS) stated that in 2019 there were 5,333 fatal occupational injuries recorded in the US alone.
With this in mind we take a look at Meili Robots’ report on the four ways mobile robotics can improve operational safety in manufacturing.
1. Improved visibility
Highlighting that the frequent cause for workplace injuries is ‘limited’’ or ‘obstructed’ visibility, those that harness sensors, LiDAR scanners, mapping and universal fleet management, can ensure that autonomous mobile robots (AMRs) can detect and respond to people and/or objects that are in their path.
AMRs can remove humans from dynamic and high risk environments due to their ability to autonomously navigate and establish the best route to get to a given destination.
2. Reduced contact with dangerous machinery
While manually-operated forklifts are one of the most common technologies used in warehouses and material handling, according to the Occupational Safety and Health Act (OSHA), there are 97,000 forklift injuries on a yearly basis.
Meili Robots comments that “with a worker getting injured on the job every seven seconds and a loss of 104 million production days due to work-related injuries in 2017, using mobile robots as an alternative will not only lower the risk of injury and death among workers substantially, but it will also keep your business moving without losing valuable production time.”
3. Automation of repetitive tasks
According to Meili Robots, 33 per cent of worker injuries in manual material handling can be attributed to lifting or lowering objects. Using AMRs reduces the risk of collisions, optimises efficiency and can reduce the risk of injuries due to repetitive lifting and lowering tasks.
4. Social distancing
With the increased need for safety in the workplace in light of COVID-19 , the use of AMRs can eliminate unnecessary contact between workers.
“Autonomous deliveries are bringing supplies to people as they adopt social distancing. Automated workstations are speeding up the work of pharmaceutical companies. Automation is on the front lines of this battle,” said the Robotic Industries Association (RIA).
For more information on manufacturing topics - please take a look at the latest edition of Manufacturing Global.