How Has COVID-19 altered Digital Transformation?
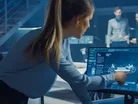
"Covid19 has forced us to unlock the potential of the investment in the collaborative tools and telecom infrastructure of the 3rd industrial revolution and imparted greater momentum to the transition towards 4th Industrial Revolution society. The pace of commoditization and automation has accelerated.” Sandeep Mishra, Director EMEA at EY
As we discussed last week in our examination of “What is Industry 4.0?” The Fourth Industrial Revolution has emerged in recent decades and involves a digital transformation focusing around robotic process automation, artificial intelligence/machine learning and blockchain. Digital transformation refers to the integration of technology in all areas of business, Manufacturing Global takes a detailed look at the impact the COVID-19 crisis has had on the acceptance of this digital transformation.
As Mishra shared in his article “Rise of Digital Artisan” the global pandemic has forced the hand of many organisations to adapt these digital alterations at a quicker pace than previously planned. Some companies have had to adapt to accept that these digital transformation measures are vital, and need to be implemented within the next few months and not over the upcoming years. These changes mean that companies are able to keep working remotely, operate factories in “Lights out” and use predictive systems to increase efficiency and lower costs.
Digital adoption is in different stages as the entire world is in various phases of recovery from COVID-19, with businesses considering prolonging remote working options which will require an investment in video software for example. This means an increased need to digitise internal operations to ensure that teams can continue their work remotely and uninterrupted. On the other hand, this sudden acceleration in digital transformation is proving a boon to some companies, as we have seen since January, Google Meet, which is free to use, grew its peak daily usage by 30 times.
Contactless and the “new normal”
As the pandemic has highlighted, public health and contactless operations are critical. Customers are able to request a contactless customer interaction with businesses, either due to the law in local areas or due to their expectations moving forward. Businesses need to show their commitment to this new way of thinking.
This contactless approach needs to go further than just in-store, with manufacturers and logistics companies requiring new technology to allow them to keep their supply chain also hands free. Companies seeking to emphasize safety should focus on designing a contactless end-to-end journey. By doubling down on ease of access and use across digital and physical channels, companies can improve both customer safety and satisfaction.
These changes can be as simple as “touch-free” packaging and online ordering capabilities for some organisations. Obviously, these changes do not happen overnight, however, there are businesses who have made these changes their priority, and the digital transformation that we are seeing is driven by these changes.
- Schneider Electric's Strategic Human-focused DigitalisationDigital Factory
- Merck & Siemens Partner on Digital Transformation TechnologySmart Manufacturing
- Digital Transformation: How to Win the Persuasion GameDigital Factory
- Manufacturing Buyers Driven Away by B2B Webstore HeadachesTechnology