How manufacturers can make their energy usage more efficient
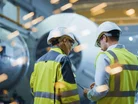
With behemoths including Unilever, Dr. Oetker, and Molson Coors helping to stock cupboards, fridges and freezers around the world, the UK has a food and drink manufacturing industry to be proud of.
But this is an industry facing challenges across multiple fronts: Brexit, the ongoing impact of Covid, the war in Ukraine, and the rising cost of energy, are forcing manufacturers to rethink their processes, increase their prices, or even both.
While many of these challenges show no signs of abating in the near term - much as we’d all like them to - there are things that these manufacturers can do now to help their situation during these trying times.
A solid foundation for food manufacturing
The current energy crisis is hitting businesses hard - they don’t benefit from cap protection like individual consumers and households do, so are particularly susceptible to increases in costs. What’s more, manufacturers overseas aren’t experiencing the same energy price shocks, meaning UK manufacturers are becoming less competitive and could miss on business opportunities out to rivals abroad due to factors beyond their control.
We estimate that approximately a third of UK manufacturers do not set energy efficiency targets nor have any means of measuring improvements.
We need to act now to make manufacturing processes more transparent, efficient and sustainable.
The main issue UK manufacturers are likely to face? They often don’t know what they don’t know.
The attitudinal shift
Before making any technological or organisation changes, it’s important to make an attitudinal shift - in particular around what energy actually is within the production process. For many, energy constitutes a lump, fixed cost, however this needn’t be the case.
A report from the University of Birmingham - Trends in Food Science & Technology (2019) - highlighted “available energy use data for food manufacture is very fragmented, and a single comprehensive database is lacking”.
Given the sheer variety of energy and fuel consumption amongst various popular foodstuffs, manufacturers should start to see their energy usage as a cost which can be cut, but only if they can gather enough understanding of where it is being used at a more detailed level.
Manufacturers must get granular with assets
Many manufacturers don’t have an asset-level understanding of energy consumption - this means they might have a view of total energy usage for a facility, but won’t know how much of this is lighting, heating, drying, or freezing of produce.
But by understanding energy consumption at a more granular level, it’s possible to identify inefficiencies and make changes - almost instantly.
We know that manufacturers keep a very close eye on operating costs - a food manufacturer such as Unilever for example, will have a very detailed view of where they get their ingredients from and how much they cost. The same can be possible for energy usage, too - by understanding it at a more detailed level, facility managers will be able to reduce the cost per unit by taking a more tailored approach to consumption.
Peak shaving is another area to look at
As well as developing an asset-level understanding of energy consumption through a platform such as Hark, manufacturers should consider ‘peak shaving’. Essentially, manufacturing companies are frequently subjected to peak-load-dependent energy prices/tariffs, so facilities are faced with high costs for the peak consumption utilised, rather than their total consumption.
The reduction of this energy peak, known as peak shaving, has proven to reduce electricity bills by 10-30%.
This was a particular challenge one of our non-food manufacturing clients came to us to resolve. Working with Hark we helped to reduce the performance variance of a production line in a manufacturing facility, helping to highlight the potential to reduce energy costs by 10%, saving over 60,000 kgC02e. By highlighting energy spikes we can uncover system inefficiencies in order to optimise shift changeovers to reduce costs.
Utilising technology is the quickest and most cost-effective way of improving efficiency across manufacturing
The Hark platform is an example of how cutting-edge technology can work alongside legacy manufacturing assets to identify and solve inefficiencies.
The cloud-based sensor platform, powered by Intel Gold, allows production facility managers to get an asset-level understanding of energy usage, meaning they can spot inefficiencies and trial different things to reduce energy consumption without impacting the quality of the product.
One of the best things about the Hark platform is its versatility, and compatibility with everything from vast, complicated production operations spanning numerous sites, to one-off, niche facilities.
Many manufacturers can be impeded from making technological changes due to perceived high costs of implementing change.
But this is seldom the case - from our experience, pretty much every manufacturer in the UK could save on their energy usage, they just need to get better at measuring their energy use.
Start small (but think big) for the future of energy in manufacturing
Faced with monitoring huge, complicated manufacturing facilities can be daunting - for facility managers and procurement specialists alike - but it doesn’t need to be.
The most important thing is getting started - this may mean focussing on a single element of one aspect of the production process, at one facility.
By testing, learning and adapting, it’s possible to identify inefficiencies in one area before rolling out changes throughout the entire production line. A segmented and evolving approach to manufacturing energy efficiency is the smartest way to make improvements without sacrificing on the quality of produce.
Thankfully, the UK has a brilliant track record of not just producing things which change the game, but doing so in a way which is equally as innovative.
Byline written by Jordan Appleson, Founder & Chief Executive Officer at Hark
- Siemens, Sony & NVIDIA Unveil New Industrial AI Tools at CESAI & Automation
- Manufacturing Unwrapped: Inside IKEA, The Wonderful EverydayProduction & Operations
- Carbmee: Helping Maersk & Coca-Cola Curtail Carbon EmissionsSustainability & ESG
- EY: How Technology Can Power Green ManufacturingSustainability & ESG