10 Smart Manufacturing Adoption Challenges
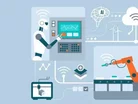
Looking to implement a smart manufacturing project within your organisation?
Manufacturing global takes a look at the 10 most common challenges experienced by manufacturers when it comes to smart manufacturing projects.
For more information on manufacturing topics - please take a look at the latest edition of Manufacturing Global.
10: Lack of Clear Goals, Objectives and Justification
When looking to implement a smart manufacturing project it is important to get the basics right. It is important that those implementing the project know exactly what is required, the objectives and the business benefits for the project.
“Even if it’s cool technology and the project is under budget and ahead of schedule, if it doesn’t produce real business benefits, then the project’s a waste of time and money,” says John Clemons, MES Solution Consultant at Rockwell Automation.
09: Misunderstanding of the Requirements
SImilar to the goals, objectives and justifications, it is also important to outline and document the project requirements, reviewing them with team members in the business.
"Requirements for any project, and smart manufacturing projects are no exception, must be driven by the business and must have a clear business case," says John Clemons, MES Solution Consultant at Rockwell Automation.
08: Lack of Buy-In
Now that the goals, objectives and justifications are laid out, it is then important to have employee buy-in from those involved and those that will be using the solution.
“You must get their buy-in, or the project just won’t be successful,” says John Clemons, MES Solution Consultant at Rockwell Automation.
07: Funding
“Smart manufacturing projects are rarely funded to the degree they need to be, simply because it seems like there’s always something that gets left out,” says John Clemons, MES Solution Consultant at Rockwell Automation.
It is important that manufacturers detail all internal and external resources required, making sure that they align with the project’s budget.
06: Timing and Schedules
Realistically, John Clemons, MES Solution Consultant at Rockwell Automation says that, “the project really will probably cost more and take longer than you want or expect.” Therefore it is important to make informed decisions based information acquired relating to the project at each step of the process.
“Scope creep happens all the time and must be managed. It probably happens more with smart manufacturing projects. If you want to increase the scope, just make sure you increase the budget and schedule to match,” adds Clemons.
05: Requirements and/or the Business Environment Changes
It is no secret that business environments can rapidly change, and this is particularly true for the manufacturing industry. It is important to implement flexibility into the project objectives and requirements in order to make it adaptable to changing environments.
04: No Leader Driving the Project and Lack of Commitment
“This is pretty common,” says John Clemons, MES Solution Consultant at Rockwell Automation. “There must be a champion — someone who drives the smart manufacturing project forward and is focused on the business processes and the business benefits.”
Often project commitment depletes over time, having a ‘champion’ can help with this, as well as approaching the project in steps that showcase the individual successes along the way.
03: Lack of Understanding of Business Processes
Similar to understanding the goals, requirements and justifications for a smart manufacturing project, it is also important to ensure that those involved know the business process and how a smart manufacturing solution fits into the processes.
02: Misunderstanding Technology
Following on from the lack of understanding when it comes to business processes, it is important that all involved understand the capabilities of the technology in order for it to be used correctly, achieve the promised benefits and be successfully adopted within the business.
01: Having the ‘Solution’ Before the Requirements
“This happens way too often. Someone has the solution or technology already figured out before the business requirements are even talked about. This is nothing but a recipe for disaster, but that doesn’t mean that it’s easy to avoid,” says John Clemons, MES Solution Consultant at Rockwell Automation.
It is important for manufacturers looking to implement a smart manufacturing project to be aware of this, and direct the conversation back to the business needs.