Moody's: how Manufacturers can Mitigate Supply Chain Risks
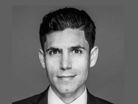
In a time of substantial supply chain instability and disruption, Manufacturing Digital spoke to Enrico Aresu, Compliance and Financial Crime Industry Practice Lead for the DACH and central-eastern Europe regions, Moody’s about how manufacturers can mitigate risk and get ahead.
What is the current regulatory state of play manufacturers need to be aware of?
Since the start of the 2010s, several supply chain-based regulations that manufacturers may have to comply with have been enacted, as governments look to reduce funds flowing to entities that damage the environment, or are engaging in modern slavery.
The German Supply Chain Due Diligence Act, Australia’s Modern Slavery Act: 2024 Amendment, and the European Union’s (EU) Corporate Sustainability Due Diligence Directive all have broad multi-national scopes. Failure to comply with these regulations can lead to fines, reputational damage, and costly delays across supply chains. Adherence is a persistent challenge, given the global nature of many supply chains.
Germany’s Supply Chain Due Diligence Act, introduced in 2023, is among the most comprehensive regulations, requiring manufacturers with a presence in Germany to implement “appropriate measures” to respect human rights and the environment. The environmental provision adds complexity, as firms must find a way to account for the environmental impact of their supply chains to report effectively. This requires organisations to gain visibility into every supplier’s operation within their chain and is no mean feat.
Manufacturers based in the UK have several supply chain provisions to be aware of. The Modern Slavery Act, introduced in 2015, requires businesses to produce a slavery and human trafficking statement each financial year, setting out the steps they have taken to ensure their global supply chain is free from modern slavery.
Similar requirements for consideration of human rights are also present in the US, where a number of regulations and agreements address forced labour. For example, the United States-Mexico-Canada Agreement (USMCA) states that US authorities will stop goods made in whole, or in part, by forced labour from being imported.
What supply chain risks do manufacturers need to be aware of and what are their consequences?
Manufacturers need to be aware of a variety of risks within their supply chains. Sanctioned entities, forced labour in operations, and organisations with poor financial health can all present risks in a global supply network.
Not having a robust approach to third-party risk management can result in a range of outcomes, from large fines to significant reputational damage.
The growing number of sanctions and therefore sanctioned entities in recent years
represent a significant supply chain risk. While reputational damage is an important factor here, manufacturers also need to consider the threat of significant fines and pauses to business operations resulting from engaging with a sanctioned entity.
Money laundering is another widespread concern that, although generally less of a focus in regulatory texts, is often linked to forced labour and instances of fraud.
How prevalent are these risks?
Manufacturers essentially now operate in an era of exponential risk, with the number of interconnected threats rising across the globe. For instance, data from Moody’s Grid database found that modern slavery incidents rose nearly 17% in the EU from 2022-2023 and have nearly doubled in the UK in the last five years. The UK also plays host to the highest rate of money laundering in Europe, accounting for almost 30% of incidents.
Manufacturers have been exposed to greater risks since Russia’s invasion of Ukraine in 2022. Before the invasion, sanctions compliance was limited to a list-checking exercise for a small number of companies.
Now, amid increased sanctions, manufacturers need a more sophisticated approach that encompasses ownership and influence over entities. This is especially important as sanctioned companies embrace innovations to avoid detection, such as Russia’s ‘shadow fleet’ for selling oil and gas.
Any single entity in a network of providers of goods, services, and parts can represent a risk to operations and disruption to supply chains.
What tools can manufacturers use to help de-risk their supply chains?
Navigating these risks can seem daunting, but it begins by asking the right questions – starting with, who am I doing business with? When onboarding suppliers or monitoring risk, it’s vital for firms to ask: what company information do we need? What regulatory risks are involved? Can we do business with this supplier? Do we have a view on their financial stability? And who are their suppliers?
De-risking is a continuous process, not simply one for onboarding. Manufacturers need to monitor for key red flags on a continual basis, integrating data checks to create an evolving profile of risk accounting for different factors. If a supplier’s risk profile changes, manufacturers need to know about this in real-time to minimise disruption and the threat to the organisation – perhaps even moving to off-board a supplier, which comes with its own set of risk assessment procedures.
It's crucial to recognize that while switching suppliers may mitigate certain risks, it introduces new ones, necessitating a strategic approach to supplier risk management. Incorporating a 'value at risk' model into the supply chain and operational risk management can significantly enhance the ability to prioritise risks. By quantifying the potential financial impact of supply chain disruptions, manufacturers can make informed decisions on where to allocate resources and which risks to address first.
This approach not only aligns with the regulatory compliance efforts but also supports a more resilient and efficient operation by focusing on the most impactful risks. This strategy offers a comprehensive risk overview, aiding manufacturers in maintaining operational integrity while navigating complex regulations.
There are tools businesses can use to understand their risk exposure and reduce it, while also simplifying visibility over risk in their supply chains.
Holistic offerings account for significant factors such as who the ultimate beneficial owners of a business are, whether there are sanctioned entities in the supply chain, and whether there are issues with a provider due to working practices or the location of operations. Getting a unified view of risk provides the best chance of understanding and mitigating supplier-related risk before it causes disruptions.
Manufacturers can seek automated solutions that assemble risk profiles based on key factors like sanctions exposure, money laundering risk, flags for forced labour, and jurisdictional anomalies, rather than trying to manually keep check on these materially important yet changing risk-related criteria.
Ultimately, the right approach to third-party risk management will vary from business to business. An automated, data-driven, risk-based approach that comprehensively covers compliance with applicable regulations can provide the starting point from which manufacturers are best able to monitor their supply chains according to their risk appetite most effectively.
How can a manufacturer best assess the risk associated with an entity layers down in their supply chain?
Firms need to adopt a risk-based approach that incorporates a robust due diligence process, with solutions that enable them to create a level of transparency in their supplier network. One major challenge to building this risk-based analysis is the fragmentation of data, especially for manufacturers that use a wide range of tools, data sets, and processes across their supply chain operations.
Large businesses will likely have multiple systems involved with risk and compliance planning, separating data points. Ideally, companies would have a unified view of risks across their supplier ecosystem.
With automated access to quality datasets integrated into analysis processes, checks can be carried out on any company worldwide to create more transparency and enable better decision-making. Automated systems can help reduce the workload on those responsible for mitigating the risk within a supply chain, speeding up processes where delays to time-sensitive decisions could cause major problems.
When third-party risks are identified and controlled in this way, manufacturers can make more informed risk-based decisions about who they work with and how they comply with regulations.
Make sure you check out the latest edition of Manufacturing Digital and also sign up to our global conference series - Manufacturing & Mobility LIVE
Manufacturing Digital is a BizClik brand
- The Sustainable Start-Up Behind Evri's Green PackagingSustainability & ESG
- Evaluating China's Involvement in UK Wind ManufacturingSustainability & ESG
- SHEIN & The Sustainability Challenges of Fast FashionSustainability & ESG
- Covestro & DB Cargo Drive Sustainable Polymer TransportationSustainability & ESG