Rockwell & Royal Mint: Extracting Gold From E-Waste
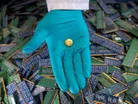
Electronic waste is one of the fastest-growing waste streams in the world. According to UNITAR staggering 62 million tonnes of e-waste was produced in 2022, an increase of 82% from 2010. That’s enough to fill 1.5 million 40-tonne trucks. That’s enough trucks to form a bumper-to-bumper line around the equator.
E-waste is a major environmental and health hazard, containing toxic additives and hazardous substances like mercury. These chemicals can damage the human brain and coordination system, having a profound impact on the health of the people, primarily children, who scavenge through them for money.
In hellish graveyards of e-waste- dumped in less economically developed countries in Africa, Asia and the Middle East- children pick through toxic waste, searching for trace amounts of silver, gold, copper and other precious metals used in devices.
To access these metals they manually dismantle them into component parts or even burn them, inhaling toxic fumes from rubber. With no real economic opportunity, they are forced to take this risk to survive.
In 2030, an estimated 82 million tonnes will be produced. Electronic waste is rising not only five times faster than documented e-waste recycling but also three times faster than the world’s population.
Every year consumers chuck away existing models- laptops, consoles and phones- to chase something shiny and new, and this global crisis only gets worse.
To even begin tackling this problem, improved recycling and recovery infrastructure is needed, in addition to a fundamental rehaul of how manufacturers approach material extraction, usage and disposal.
Rockwell Automation is working to make progress in this area, partnering with The Royal Mint to make its gold extraction process more sustainable through technology.
The Royal Mint
The Royal Mint, founded in 886 AD, is the UK's official mint and one of the oldest organisations of its kind in the world.
It produces all of the nation’s coins, creating commemorative coins, medals, and bullion products.
Historically located in the Tower of London, it moved to Llantrisant, Wales, in 1968.
Known for its craftsmanship, innovation, and commitment to quality, the Royal Mint has expanded into precious metals investment and heritage experiences, preserving the UK’s monetary history whilst evolving into a global leader in coinage and precious metal services.
The company’s new Precious Metals Recovery Facility using Rockwell Automation’s PlantPAx® Distributed Control System (DCS) to better manage and control the gold extraction process.
How PlantPAx® DCS is tackling E-waste
One of the core ways PlantPAx® DCS tackles e-waste is through rare earth element extraction.
The PlantPAx DCS at The Royal Mint’s facility monitors and controls a chemical extraction process that removes gold from printed circuit boards found in discarded laptops and mobile phones.
This extraction technology, which was only at lab scale a few years ago is now successfully scaled and operational at The Royal Mint’s site in Llantrisant, Wales.
Methods to recycle and repurpose the e-waste are being explored by Rockwell and The Royal Mint at the facility, as they both pursue greater circularity.
“The successful collaboration with Rockwell and the deployment of its DCS solution allowed us to demonstrate the technical viability of the technology to operate at scale,” says Tony Baker, Director of Manufacturing Innovation at The Royal Mint.
“This puts us firmly on the road to our 4,000-ton per annum target, and discussions are already well underway with regards to usage of the recovered materials, as are the plans to expand the technology further.”
This process not only reduces the amount of e-waste but also offers an alternative extraction method to mining, which has its own host of sustainability and ethical problems.
While this extraction impacts children’s ability to profit from the e-waste, it also in turn de-incentivises scavenging and exposure to toxic chemicals.
In the ensuing rift, economic opportunities must be created through close collaboration between local communities and the government, breaking the current exploitative evil of the e-waste cycle.
Make sure you check out the latest edition of Manufacturing Digital and also sign up to our global conference series - Manufacturing & Mobility LIVE
Manufacturing Digital is a BizClik brand