4 ways Industry 4.0 makes factory maintenance easier
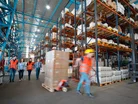
Manufacturing firms heavily rely on machinery to produce their goods, making proper factory maintenance a critical aspect of their operations. However, implementing a robust maintenance program can be a challenging task that requires a significant amount of resources, including time, effort, and capital costs.
Over the last decade and a half, the growth and advancement of Industry 4.0 technologies have ushered in a new era of technological innovation and transformation, particularly in factory maintenance. Workers now have access to a myriad of novel tools and techniques, facilitated by the technological cornerstones of Industry 4.0 — the Internet of Things (IoT), Artificial Intelligence (AI), and Machine Learning.
The advantages of these solutions, however, go far beyond just operational savings. By optimising maintenance operations, firms can enhance worker safety and reliability while reducing their environmental impact through improved sustainability measures. This comprehensive approach to maintenance represents a larger movement in the manufacturing sector — one that recognises the significance of balancing economic, social and environmental concerns in the pursuit of longer-term success.
In this article, we will explore four ways how Industry 4.0 simplifies the planning and implementation of factory maintenance strategies.
#1: Predictive maintenance
Predictive maintenance plays a crucial part in the early detection of equipment failure and optimising maintenance scheduling. Through advanced analytics and machine learning algorithms, predictive maintenance techniques monitor equipment performance in real time, enabling the identification of potential issues before they escalate into significant problems. This proactive approach allows maintenance teams to address equipment issues promptly, mitigating unexpected downtime that can be costly and disruptive.
Industry 4.0 has introduced several use cases for predictive maintenance, including:
- Monitoring vibration levels in rotating equipment, such as motors and pumps, using sensors. If the vibration levels exceed a certain threshold, the equipment is scheduled for maintenance
- Employing temperature sensors to monitor the temperature of electrical components, such as transformers and motors windings, or rotating equipment like bearings. If the temperature exceeds a certain limit, maintenance is scheduled to prevent equipment failure
- Utilising acoustic sensors to monitor the sound produced by equipment, such as compressors and turbines. Changes in sound can indicate potential problems and prompt maintenance actions.
#2: Digital twins in manufacturing
Digital twins are virtual replicas of physical equipment, processes, or systems, enabling the simulation and optimisation of maintenance procedures. They provide a digital model of equipment that can be used to test maintenance procedures and predict maintenance requirements.
In Industry 4.0, digital twins have found various applications, including:
- Virtual testing and simulation: maintenance teams can simulate and test equipment performance in a virtual environment. This allows planning and evaluation of maintenance tasks before they are performed on actual equipment. Virtual testing and simulation can help reduce downtime and improve the precision of maintenance activities
- Remote monitoring and control: maintenance teams can monitor and control equipment performance remotely. This enables maintenance tasks to be performed remotely, reducing the need for on-site maintenance and improving worker safety
- Training: Digital twins serve for training and education purposes. Maintenance teams can learn how to perform maintenance tasks in a virtual environment, reducing the reliance on on-the-job training while also improving worker safety.
Some of the manufacturers using digital twins include corporations such as IBM, General Electrical and ANSYS. They leverage this technology both internally and by involving their client base, enriching the overall experience and providing advanced solutions.
#3: Collaborative robots & factory maintenance
Collaborative robots, commonly known as "cobots," are another key aspect of Industry 4.0 that can make factory maintenance easier, safer and more efficient.
Here are a few examples of their applications:
- Inspection and diagnosis: cobots can be used to inspect and diagnose equipment issues. For example, a cobot equipped with a camera can inspect equipment components to identify signs of wear or damage. This enables maintenance teams to detect issues early on and perform maintenance tasks before they escalate into larger problems
- Collaboration with humans: cobots can work collaboratively with maintenance personnel to perform maintenance tasks. For example, a cobot can hold a tool while a maintenance worker completes a task that requires both hands. This can increase the productivity of maintenance jobs while decreasing the risk of injury to maintenance workers.
#4: Augmented reality in factories
Augmented reality (AR) is a technology that enhances the physical world by incorporating digital elements such as visuals, audio, or other sensory inputs, usually through the use of wearable devices. By providing real-time information on equipment performance, maintenance processes, and safety protocols, augmented reality can significantly improve maintenance practices and programmes.
Examples of augmented reality in Industry 4.0 include:
- Remote assistance: AR can be used for remote assistance, allowing maintenance teams to connect with experts who can guide them through maintenance tasks. By wearing AR glasses, a maintenance technician can receive instructions and visual aids from a remote expert who can see what the worker sees. This reduces the need for on-site expertise, saves money on travel and increases maintenance efficiency
- Equipment visualisation: AR can visualise equipment components and provide information on their function, performance and maintenance requirements. For example, an AR headset and glasses can overlay digital information onto a physical equipment component, such as highlighting the location of a hidden valve within an assembly or presenting an instant snapshot of maintenance history information in the field. These functionalities assist maintenance employees in performing maintenance tasks more efficiently and precisely
- Training: AR can be used for training maintenance personnel on equipment maintenance procedures. For example, an AR headset can provide step-by-step instructions for intrusive maintenance tasks such as a pump overhaul, with visual aids and interactive elements. This helps reduce training costs, improves learning outcomes, and ensures that maintenance personnel are properly trained to perform maintenance tasks.
Industry 4.0 has revolutionised maintenance practices in factories by harnessing technologies such as IoT, AI and machine learning. These advancements have made maintenance tasks more efficient and cost-effective. By implementing the four strategies discussed in this article, factories can further optimise their maintenance processes, minimise downtime and increase productivity.
It is essential to acknowledge that adopting these technologies and strategies requires a significant investment of time and resources. However, the long-lasting benefits they offer outweigh the initial costs. Industry 4.0 technologies empower factories with higher flexibility and adaptability to meet changing market demands. By embracing these new technologies and strategies, factories can unlock the full potential of their operations. The future of maintenance is here and it is up to factories to take advantage of it.
- The University Manufacturing Circuit Boards from LeavesSustainability & ESG
- Schneider Electric's Commitment to Sustainable ManufacturingSustainability & ESG
- Lenovo & Saudi Alat Building Green Manufacturing FacilitySustainability & ESG
- Nissan Brings Biodiversity to the Factory through RewildingSustainability & ESG