EOS’ Spencer Thompson on the benefits of 3D printing
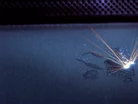
Hi Spencer, please introduce yourself and your role.
“Hello, I’m Spencer Thompson and I’m passionate about all things additive manufacturing (AM) and solving complex engineering problems. I’m the Lead Engineer of Environmental Technology at EOS North America.”
What led you to this industry?
“I first got into 3D printing as an undergraduate at North Carolina State University (NCSU) where I worked as a model finisher at Fineline Prototyping (now Protolabs). I was captivated by all the different parts, materials, and applications that I came across. I stayed at NCSU as a research assistant in 3D printing, developing my own master’s programme specifically for additive manufacturing. I completed my master’s project at EOS in Germany and came straight to EOS North America in Austin, Texas, where I began my professional career as a process engineer.
“During my seven years at EOS North America, I’ve had the opportunity to dive into every aspect of the industry; from building benchmarks, to trainings, to leading the R&D team. Throughout this experience, I noticed a theme in my favourite projects – those with a clear purpose of improving the world around us. Additive manufacturing projects often include the added value of minimising waste, reducing emissions, or even enabling clean energy. So, now as the Lead Engineer of Environmental Technology, I look forward to focusing on sustainable applications to drive further AM adoption across all industry sectors.”
What is EOS North America?
“EOS North America is a business of EOS, providing responsible manufacturing solutions via industrial 3D printing technology to manufacturers around the world. Connecting high-quality production efficiency and reliability with its pioneering innovation. In North America we have two main offices, our training and customer experience centre, as well as headquarters based in Novi, Michigan and our technical centre in Austin, Texas.”
Tell us about the benefits of industrial 3D printing.
“The main benefit of industrial 3D printing lies in what we refer to as “purpose-driven design.” With AM, since we are building things up layer by layer, we don’t rely on traditional tooling, moulds, or machining/casting constraints, which gives us more freedom in how we design parts. Designers can focus on incorporating features or functions that serve a purpose for the end use of the part, rather than incorporating them due to a manufacturing requirement.
“Our ability to design and build quickly also addresses the climate crises. AM was created as a rapid prototyping technology and that foundation still lives on today. We can design parts, print them, test them, and iterate within a few weeks where in the past, it would have taken months or even more than a year to do the same. The rapid development of 3D printing solutions will be key in achieving carbon emission reduction targets.”
How is this more sustainable?
“Just like you wouldn’t use a hammer to cut a piece of wood, you wouldn’t and shouldn’t use additive manufacturing for everything. Conventional machining can be an efficient way to make things, and there are supply chains set up that can efficiently recycle the machining chips. So, with AM, the sustainability of an application is going to depend on the design and function of the part.
“There are, however, some key characteristics of AM that can lead to more sustainable manufacturing.
- A part designed for AM can be made with very little waste since just the material for the part is fused. The unfused powder is recycled back into the system for the next print.
- Instead of mass production, AM reduces the need for inventory holding costs and relying on uncertain market forecasts which lead to overproduction and waste.
- An amazing application for AM is in the repair of worn parts, such as a turbine blade. Instead of scrapping the whole blade because of a damaged tip, you can build back the damaged section, extending the life of the component.
- There is a positive trend in the utilisation of distributed manufacturing models, as opposed to central production plants. This allows for the reduction of shipping emissions and critical interruptions in operations because of complicated supply chains.
“On the design side, we can create parts that are:
- Lighter and stronger than the conventional, leading to reduced emissions in the life of aerospace and automotive applications due to fuel savings.
- Durable and minimise assembly requirements due to part consolidation. Weldments or assemblies can be made into one monolithic part thanks to the lack of tooling in AM.
“The most exciting opportunities for sustainability in AM are what we are still learning. We’ve seen that we can improve the efficiency of systems with more complexly designed heat exchangers, which can reduce fuel consumption and improve the output from renewable energy generation. Every day, more driven and talented people, armed with AM knowledge are coming up with new, innovative ways to push the limits of the technology and solve some of our most pressing climate concerns.”
Spencer Thompson, Lead Engineer of Environmental Technology at EOS North America
What is the impact on supply chains?
“Again, there’s some interesting opportunities for a distributed manufacturing setup to lead to more efficient supply chains. One use case is through an eyewear company in Germany called YOU MAWO. We conducted a life cycle assessment, in partnership with the Fraunhofer EMI, on YOU MAWO glasses frames and found them to have a 58% lower carbon footprint than traditionally made acetate frames. A big part of this was due to overproduction in the traditional eyewear supply chain - with AM, you can produce just what you need, when and where you need it. This will have a significant impact on other industries as well.”
Tell us about using bio-based and bio-degradable materials.
“For material sourcing, EOS focuses on three factors: the choice of polymers for 3D printing, how the polymer powders are being generated and how the qualified additive manufacturing powder is being processed on EOS systems. Depending on the choice of raw materials, the CO2e footprint for additive manufacturing powder production can be reduced by increasing production efficiency and quality to lower scrap and increasing material reusability throughout the production journey.
“Our two most recent sustainable polymer materials are the PA 1101 ClimateNeutral material and the PA2200 CarbonReduced material. PA 1101 is a bio-based material and with a smaller carbon footprint than petrol-based polymers. PA 2200 is traditionally a petrol-based polymer with an elevated environmental impact, but EOS has been able to reduce the CO2e footprint of this material by almost 45%.”
How do you define responsible manufacturing?
“For EOS, responsible manufacturing means putting our pioneering technology expertise at the service of customers to help them achieve their own sustainability goals. 3D printing combines two levers of innovation which are linked and enabled through a digital value chain: product innovation and supply chain innovation. On the product side, AM enables purpose-driven designs and customisation of products. On-demand and decentralised production as well as circularity of materials make the future supply chain more responsible.”
How is this technology innovating the designs of energy’s biggest players like TAE and Siemens Energy?
“AM is a leading solution in the energy sector because a key component of power generation technologies is managing heat. Whether you’re concentrating sunlight to create steam or creating your own fusion reaction, like TAE, you must move heat around as efficiently as possible. With AM, heat exchangers are created with higher complexities, better durability and with more advanced materials than traditional manufacturing. All these aspects help to improve state-of-the-art power generation systems, to better utilise resources put into the system and operate longer to deliver clean, reliable energy to the grid.”
What do the next 12 months hold for you and the company?
“At EOS, the topic of sustainability started as a grassroots movement, especially in North America. Now, with Björn Hannappel, our Global Head of Sustainability and his team, we are doing our homework and laying the roadmap for our future company goals. For a long time, the AM industry just said that we were more sustainable than conventional because we reuse our powder. It turns out that there are many areas where we actually aren’t all that sustainable. We are learning about these through LCA’s like the YOU MAWO case and through organisations like the Additive Manufacturing Green Trade Association, and coming up with a gameplan to address our own sustainability hotspots.
“From energy generation to carbon capture and sequestration to emissions reduction to sustainable consumer goods, there is a lot going on. My goal for this year is to fully immerse myself in the sustainability space and learn the different ways companies are creating a more responsible manufacturing future. Through attending environmental technology and climate change conferences and continuing to grow my sustainability network, I hope to get the word out that EOS is ready to help take on these challenges.”
- Mitsubishi & CH4's Innovative Solution to Farming EmissionsSustainability & ESG
- JLR's US$81m Facility Upgrade: Luxury Meets SustainabilityProduction & Operations
- Behind China's Export Ban on Critical Battery TechnologiesSustainability & ESG
- Evaluating China's Involvement in UK Wind ManufacturingSustainability & ESG